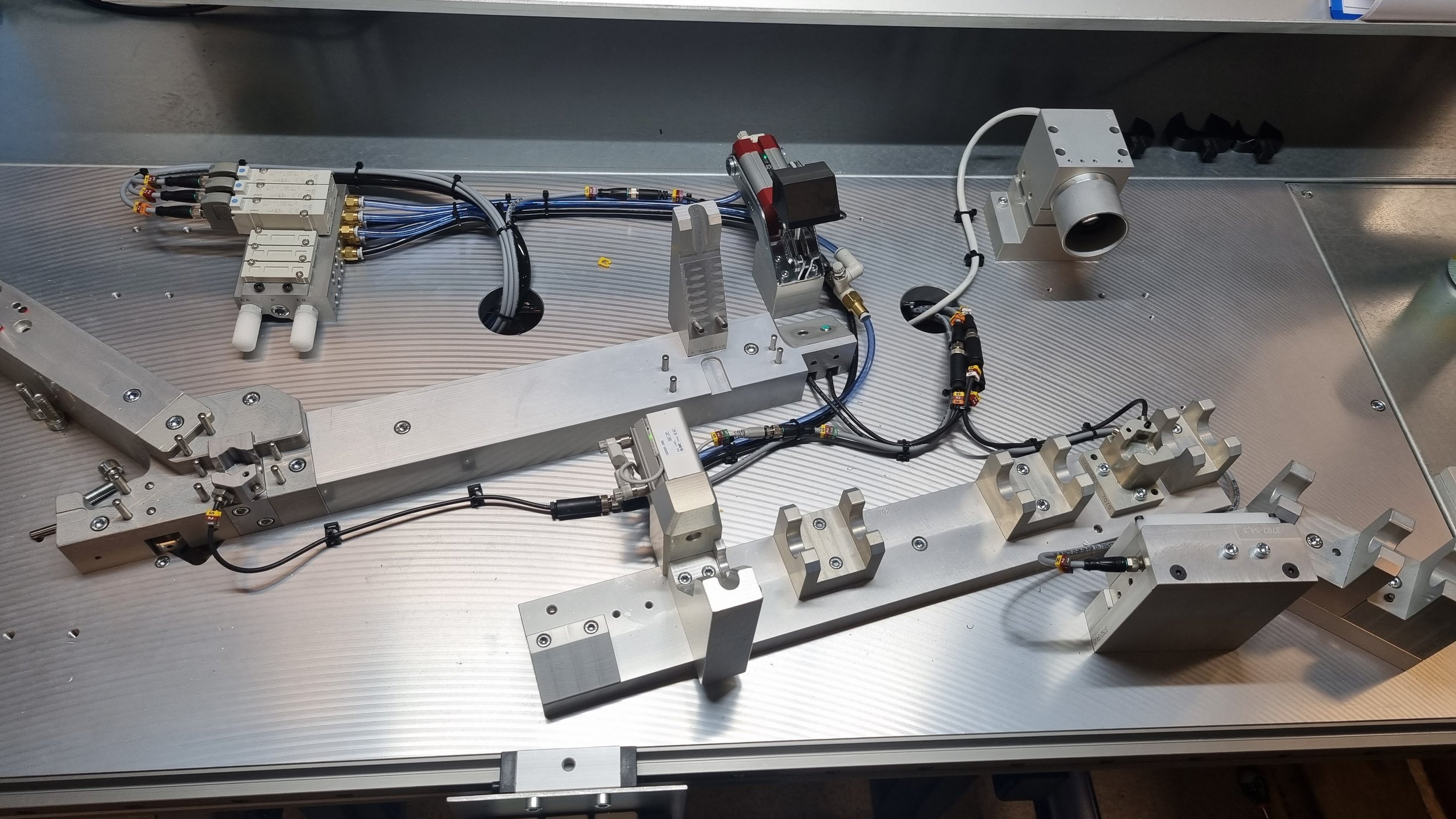
The WORKFLOW Series
HELPING OPERATORS ASSEMBLE SAFELY AND Efficiently
The automotive industry often requires complex assemblies, from precise torque applications to advanced multi-part bonding. Our WORKFLOW series is designed for adaptability, with three distinct assembly machine configurations to meet your specific needs:
WF-TM
Ideal for smaller, simpler tooling, featuring a quick-connect tooling plate.WF-TD
Optimized for larger, advanced tooling, utilizing a quick-connect tooling plate on a docking unit.WF-TI
Engineered for high-volume, integrated production with fixed tooling.
The WF-TM and WF-TD’s quick-connect systems ensure rapid and cost-effective tooling changes. All WORKFLOW machines can be equipped with integrated tools like torque wrenches and screwdrivers, maximizing flexibility and efficiency.
WF-TM Tooling, adjusted for manual installation into the machine and connected with QC
WORKFLOW TI-2-1800 advanced assembly with indexing table and 2 operator stations
WORKFLOW TD-1-1200 single station assembly machine with docking unit
For customers with low-volume part production, the “WF-TM: Battleship” offers a flexible and cost-effective manual tooling solution. This system utilizes a coordinate-based tooling plate, where the HMI guides the operator to precisely position and install part fixtures. Think of it as a dynamic, on-demand tooling setup. Part fixtures, manufactured from durable polymer with integrated guide pins, are easily placed according to the displayed coordinates.
The “Battleship” is also equipped with an I/O-Link hub, allowing for the connection of necessary sensors and ensuring accurate process monitoring.
WF-TM: Battleship
Standard features
FRAME | Adjustable working height |
---|---|
Stations | Single or dual |
Type | WF-TM, WF-TD or WF-TI |
REMOTE SUPPORT | Yes (via ethernet, 3G/4G or WiFi) |
Tooling | WORKFLOW series |
HMI | ARC ©, 19” touch-screen |
SCANNER | Barcode scanner for production orders, etc. |
ACCESSORIES & EXTRAS
Scrap box with light barriers
Label printer
Oetiker pincher tools
Torque wrench / Screwdriver
Camera verification
Automatic assembly
Cutting tool
Integrated leak testing
RFID login
ARC CONTROL SYSTEM
All machines from LANTZTECH use our in-house developed control system, ARC, enabling advanced features in a simple and easy-to-use HMI.
The ARC control system is built on an industrial PC and EtherCAT bus, featuring a large touch-screen display. The HMI presents clear textual and graphical representations of the machine’s operational status and cycle progression. Cycle steps are shown with distinct visual indicators (red/green), giving the operator a straightforward and informative overview.
With ARC, detailed statistics is a standard feature, facilitating in-depth performance monitoring. Furthermore, ARC’s flexible data communication capabilities enable seamless integration with various data management systems.