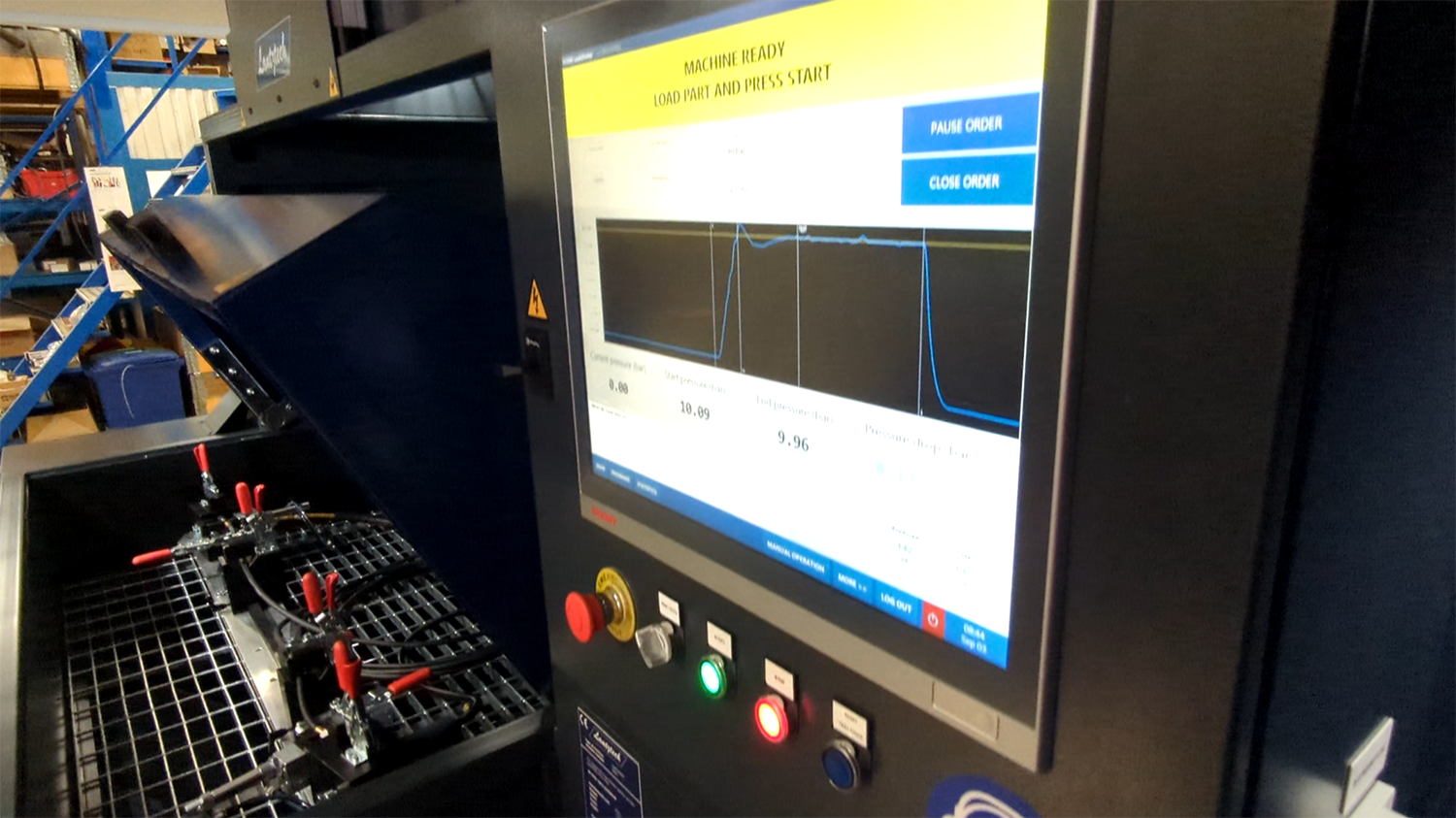
The LEAKMASTER Series
RELIABLE LEAK AND PRESSURE TESTING MACHINES for tubes and hoses
In today’s demanding automotive market, precision testing is expected. That’s why, since 1995, LANTZTECH has engineered leak testing components and equipment.
With in-house manufacturing, unparalleled control is guaranteed, ensuring consistently reliable results that meet and exceed industry standards.
Using differential pressure or mass flow sensors, the machine can be equipped with several leak testing units, enabling multiple parts to be leak tested in one cycle. The machine can be configured as a single or twin chamber machine. When twin chambers are used, one chamber can be used for part assembly, ensuring superior production flow for the operator.
The ARC software visualizes the leak testing cycle. If needed, exchangeable fixtures from the WORKFLOW series can also be used in the LEAKMASTER. We offer complete tooling with manual or pneumatic sealing, custom-made for your parts.
LEAKMASTER L-2515 with twin chambers for assembly and 3-channel leak testing
LEAKMASTER P-1140 for pressure testing up to 40 bar
Standard features
Frame | Adjustable working height |
---|---|
Chambers | Single or twin |
HMI | ARC ©, 19” touch-screen |
REMOTE SUPPORT | Yes (via ethernet, 3G/4G or WiFi) |
MAX PRESSURE | 5 bar (leak test), 40 bar (pressure test) |
TOOLING | WORKFLOW fixtures and tool plates |
SEALING | Automatic (max insertion force 3 kN) |
TOOLING | Manual or pneumatic |
SCANNER | Barcode scanner for production orders, etc. |
The standard LANTZTECH Leak testing unit is built in-house
ACCESSORIES & EXTRAS
Scrap box with light barriers
Automatic positioning system
Electric automatic safety door
Label printer
RFID login
Sealing tools for LEAKMASTER
ARC CONTROL SYSTEM
All machines from LANTZTECH use our in-house developed control system, ARC, enabling advanced features in a simple and easy-to-use HMI.
The ARC control system is built on an industrial PC and EtherCAT bus, featuring a large touch-screen display. The HMI presents clear textual and graphical representations of the machine’s operational status and cycle progression. Cycle steps are shown with distinct visual indicators (red/green), giving the operator a straightforward and informative overview.
With ARC, detailed statistics is a standard feature, facilitating in-depth performance monitoring. Furthermore, ARC’s flexible data communication capabilities enable seamless integration with various data management systems.